Table of Contents
ToggleStockouts: The bane of supply chain management
If you want to scare a distributor or a stockist, creep up behind them and whisper “stockout”.
Stockouts are often considered the biggest nuisance in the Supply Chain industry. A stockout situation occurs when a particular item in the inventory runs out of stock and is no longer available for purchase or further distribution.
Few issues have such a direct impact on sales as stockouts. When in-demand products are not available when needed, the entire supply chain is affected: from the customers to retailers to distributors to stockists, and of course the brand itself, whose reputation, not to mention profits, suffers the most. After all, if a customer does not find the brand of toothpaste they are looking for, they will likely just buy another.
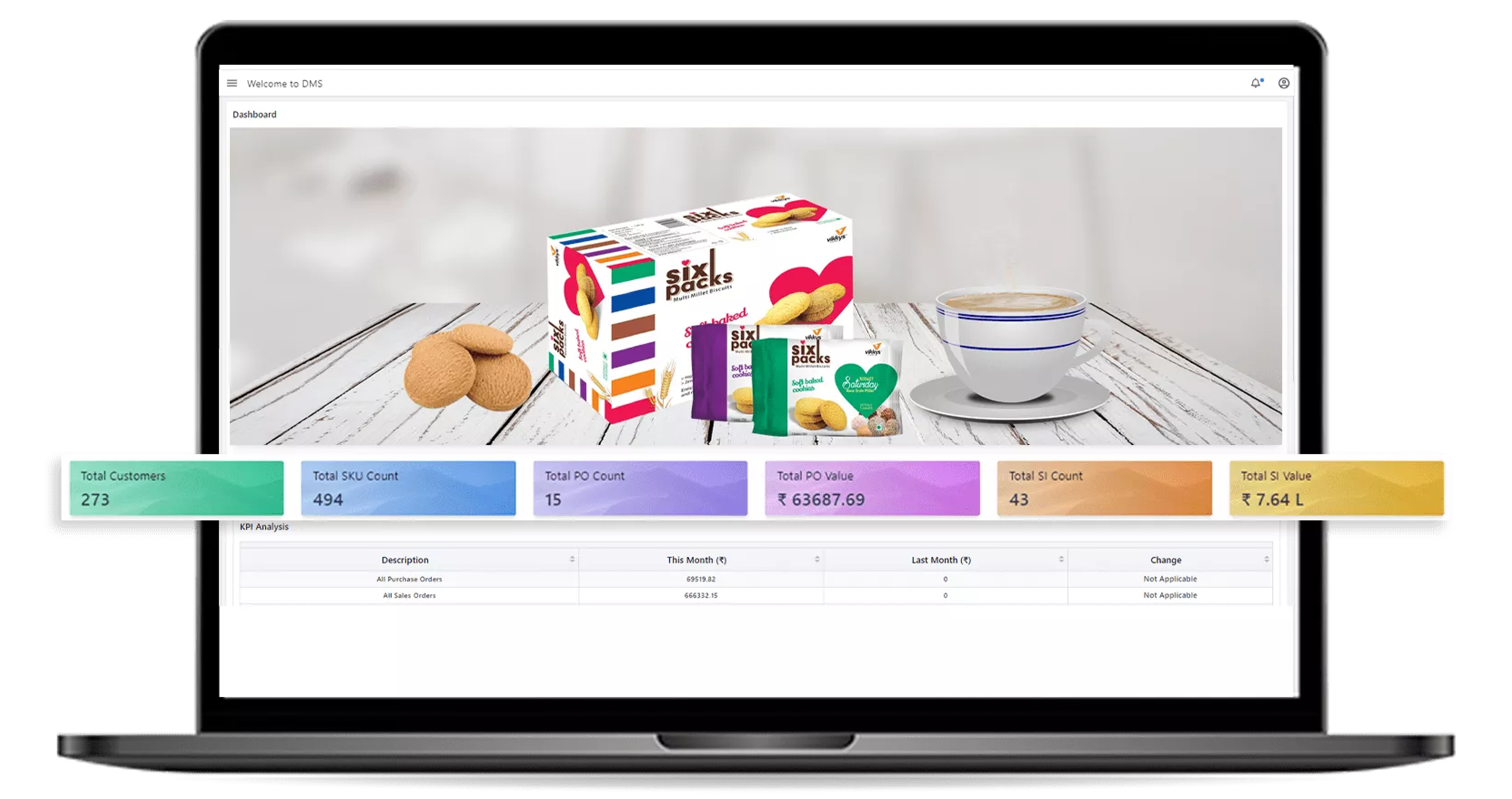
Disadvantages of manual stock replenishment
Knowing when and where to replenish stock is a key function of good supply chain management. Yet, it is also the most vulnerable. Manually refilling stock has the following disadvantages:
- Delays: Manual entries that rely on human initiative and intervention can cause delays.
- Human errors and mistakes: Everyone makes mistakes. So can the person who places the order.
- Incomplete or incorrect quantities: It is possible that the placed order does not anticipate demand correctly, or is placed for a lesser quantity that is needed, leading to even more stockouts later. On the other hand, an order placed in excess of future requirement, by over-anticipating demand, can lead to over-stocking.
- Late placement of orders: It is possible that orders are placed too late for the stock to be replenished in time.
- Time consuming: It takes time to determine the order, verify it, and then place it. And at the other end, the same process repeats.
Thus, manually replenishment of stock relies on trial and error, if that, and is extremely time consuming and wasteful.
What is Auto stock replenishment (ARS)?
Automatic replenishment of stock, however, solves all these problems. It is the future of supply chain management and distributor management, and represents a complete transformation of the traditional rules of managing inventory.
ARS represents the next step in the digital transformation of supply chain management. The true beauty of ARS lies not just in automating the process of replenishing stock, but in also intelligently determining the parameters associated with the placement of orders.
How Automated Stock Replenishment works
Auto stock replenishment (ARS) harnesses the power of machine learning and AI algorithms to forecast future demand for a product based on past sales. By analysing historical sales data, ARS predicts how much stock will be required, and when. It then uses this information to place orders automatically – without any manual intervention required.
This essentially means that the entire process is not just fully automated in the truest possible sense, but also intelligent.
Here is how a sample ARS process works:
- ARS analyzes data from hundreds or thousands of orders, historical sales figures, and usual time taken to replenish orders
- As soon as a product is about to go out of stock, it places an order at the appropriate time for the appropriate quantity
- The new stock arrives almost as soon as the existing stock is depleted
Thus, the entire process is automated end to end – complete supply chain automation.
Advantages of ARS
ARS injects not just automation into your logistics – but also intelligent decision making, empowered by the best AI algorithms. ARS directly brings the following advantages to your supply chain:
- Non-stop supply: Never run out of stock! This includes a built-in safety stock buffer.
- Improved customer satisfaction and retention: Customers are satisfied since their favorite products are always available in stock. No customer wants to buy a brand that’s repeatedly unavailable.
- Increased revenue: Stockouts can directly lead to loss of revenue and commissions. ARS minimizes the risks of stockouts, and thus loss of revenue.
- Increased Efficiency: Orders are placed instantly and automatically at the right time, so you don’t really need to do anything at all.
- Increased accuracy: Orders are placed more accurately – both in terms of quantity and timing.
- Decreased costs: Manual labour costs are minimized since logistics requirements are anticipated in advance by the system. By maintaining optimum inventory levels at all times, waste and inefficiency are minimized. This frees up time for you to focus more on other, more important tasks.
- Decreased possibility of mistakes and human errors: Since the Machine Learning algorithms learn on-the-go from previous order placements, the possibility of error is significantly reduced.
- Reduced storage and logistics costs: Since orders are placed more accurately with fewer errors, you don’t need to spend more on storage and transport than the minimum required level.
- Reduced overstocking: Overstocking is as bad as understocking and stockouts. It leads to waste and more expired products in your inventory. ARS virtually eliminates these risks, leading to fewer product returns.
Less vulnerability to seasonality: Since inventory forecasts are based on past orders, seasonal trends in sales can be anticipated accurately, and orders placed accordingly. The ARS system can also account for seasonal schemes and promotional offers run by the brand.
Conclusion
In today’s digitized, technology driven world, the purpose of a Distributor Management System (DMS) is not just to keep the lights ON. A DMS is now a driver and direct contributor of business transformation, revenue growth, and competitive differentiation. This makes ARS not just optional but indispensable for brands and distributors.
About Post Author
Nikhil Aggarwal
Driven by his passion for growth through automation, Nikhil takes pride in embarking his clients through a transformational journey and helps them be a more resilient, agile, and future-ready brand.